Polyphenylene Oxide Injection Moulding (PPO)
Polyphenylene Oxide (PPO), also known as polyphenylene ether (PPE) is a non-crystalline, high-performance thermoplastic. Known for its exceptional thermal stability and high impact strength, PPE plastic is suitable for components exposed to extreme conditions. Polyphenylene oxide is often used for electrical components in high-heat applications due to its excellent resistance to heat distortion.
This page is for informational purposes only. Fern Plastics provides injection moulding services and does not supply the material.
Polyphenylene Oxide Properties
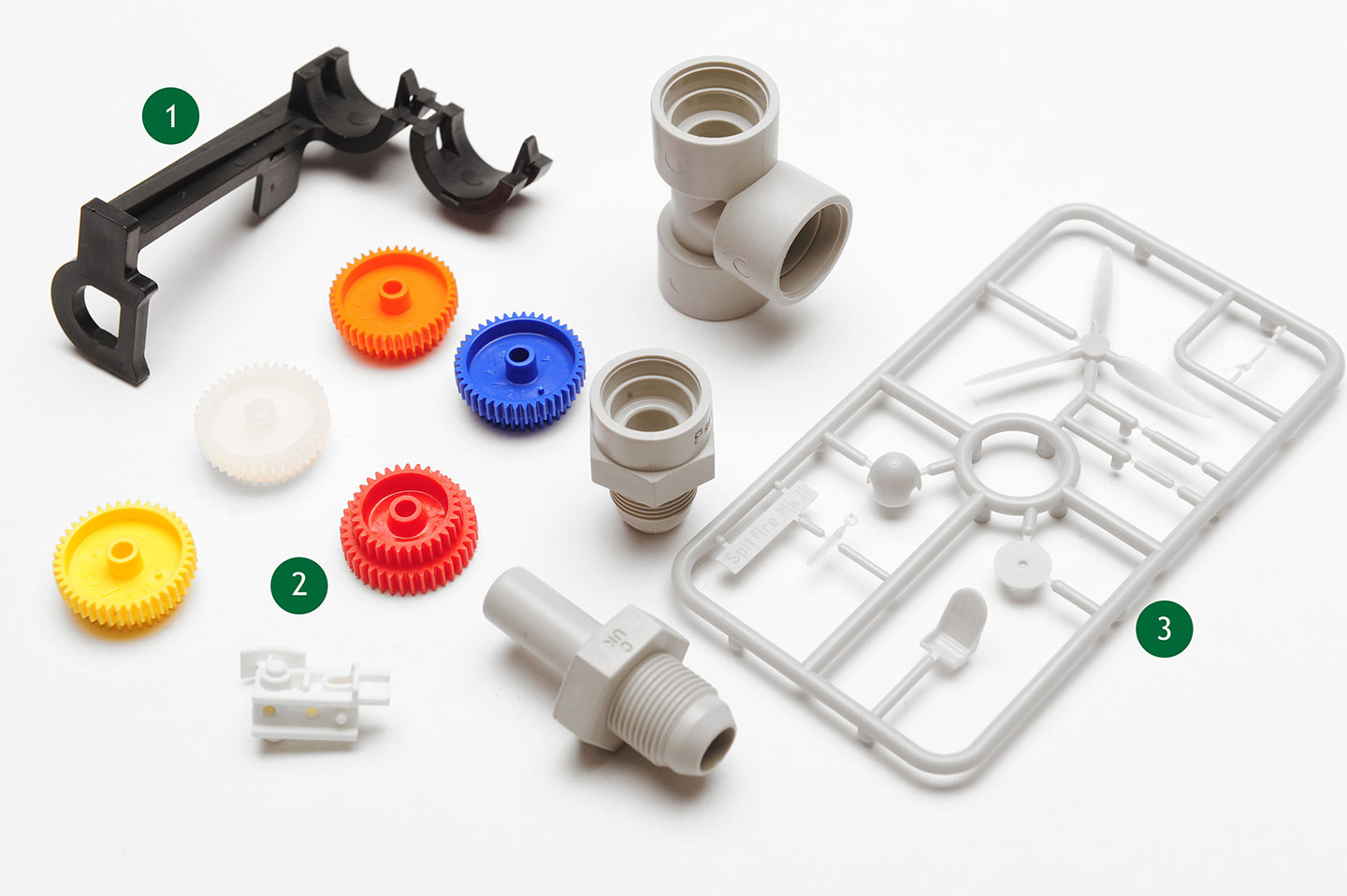
Polyphenylene oxide is a key engineering plastic with a variety of properties that make it a beneficial choice for demanding injection moulding applications. In addition to properties like chemical and flame resistance, PPO material can be blended with other materials to further enhance features like impact resistance while reducing costs.
- Thermal stability
- Dimensional stability
- High impact strength
- Excellent dielectric properties resulting in high insulating resistance
- Heat and flame resistance
- Chemical resistance
- Low relative density
- Low water absorption
Noryl – A PPO Blend for Enhanced Applications
Noryl, a modified polyphenylene oxide, is a blend of PPO and polystyrene (PS). Noryl PPO offers additional benefits that make it ideal for specific applications. Noryl resin combines PPO’s thermal and chemical resistance with improved processability and cost efficiency.
Key Advantages of Noryl:
- Low moisture absorption for excellent performance in humid environments.
- Outstanding electrical insulation properties for electronics and telecommunications.
- High strength-to-weight ratio, making it lightweight yet durable.
Common Applications of Noryl:
- Automotive parts, including battery housings and fuel system components.
- Electrical housings and switchgear.
- Water management systems such as valves and pumps.
- By leveraging the properties of both PPO and PS, Noryl expands the versatility and performance of injection moulded parts.
Benefits of Using PPO Material in Plastic Injection Moulding
Choosing PPO material for plastic injection moulding can provide manufacturers with a range of advantages from design flexibility to enhanced product performance. Using PPE plastic for injection moulded parts can also enhance product lifespans with impressive chemical and thermal resistance. As an amorphous thermoplastic, polyphenylene oxide is strong with dimensional stability across a varied range of temperatures making it beneficial when heat resistance is essential.
- Non-toxic
- Recyclable
- Transparent
- Low shrinkage
- Good load-bearing qualities at high temperatures
- High heat distortion resistance
- High strength-to-weight ratio
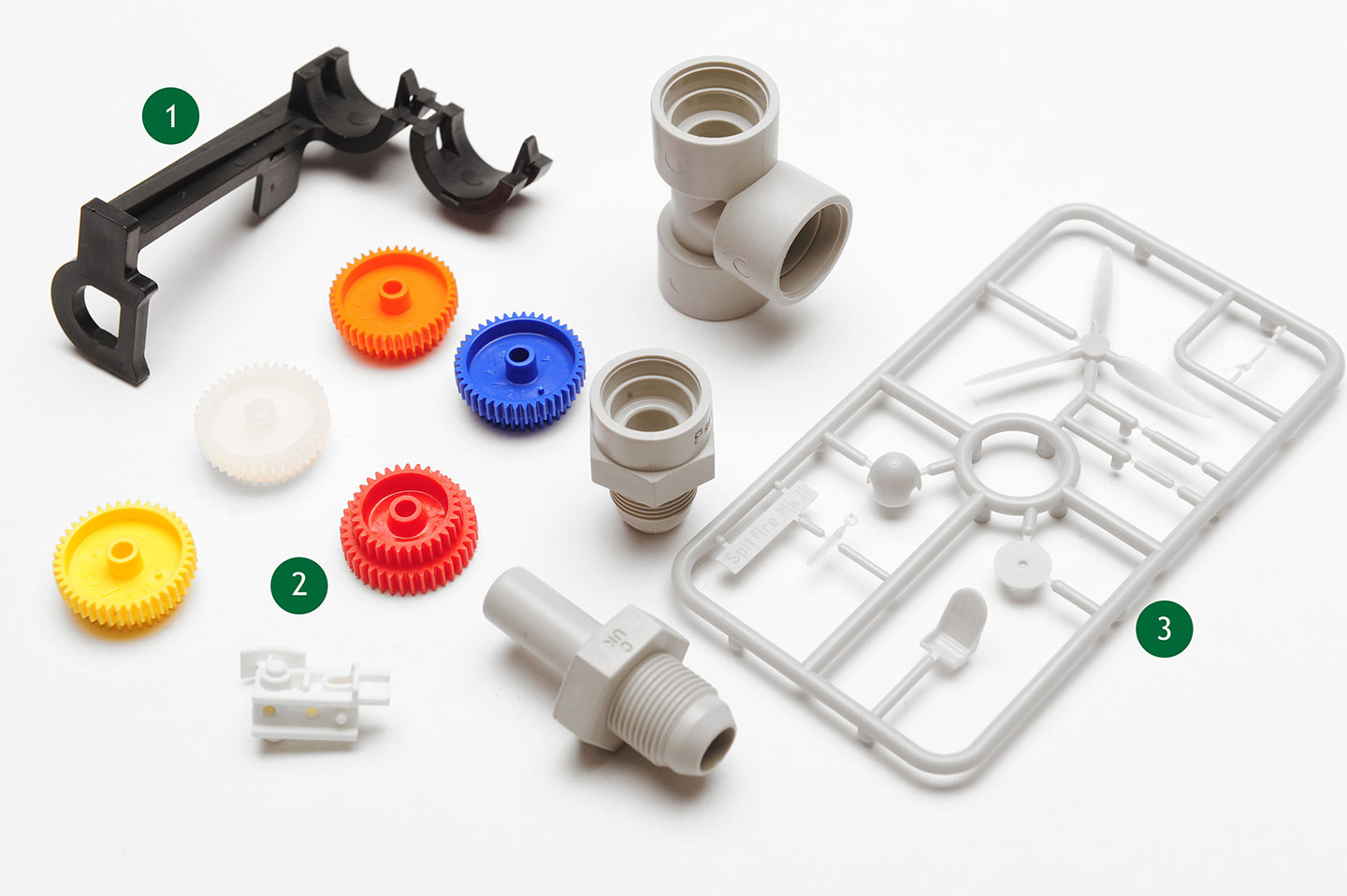
Common PPO Plastic Uses
The versatility of PPO plastic in the plastic injection moulding process makes it a useful material across a broad spectrum of industries. Its resistance to solvents and acids make it ideal for challenging environments while its stability makes it excellent for structural components.
- Housings and internal components for electrical equipment
- Pump filters
- Shock absorbers
- Computers
- Circuit breakers
- Air conditioning units
- Television components
Disadvantages of Polyphenylene Oxide
Plastic injection moulding with polyphenylene oxide plastic has a few disadvantages that can negatively affect the process. Factors like UV instability and the materials’ tendency to become a thermosetting plastic when stored for long periods are some of the disadvantages manufacturers should be aware of.
- Low fatigue resistance
- Poor fluidity
- It can cost more than other resins
- High melt viscosity
- When exposed to UV light, uncoloured PPO can become yellow
Using PPO Materials for Your Plastic Injection Moulded Project
Known for its exceptional thermal stability, chemical resistance, and lightweight properties PPO or PPE is an excellent choice for plastic injection moulding applications. Whether you’re creating intricate components for the automotive or parts for electronics PPO plastic offers reliability and versatility for high-performance applications.
To learn more about how PPO can enhance your plastic injection moulding project, contact Fern Plastics online or call 01902 758282 to speak with our team of experts. We’ll guide you through the best material choices for your specific needs.
Polyphenylene Oxide Injection Moulding (PPO)
Polyphenylene Oxide (PPO), also known as polyphenylene ether (PPE) is a non-crystalline, high-performance thermoplastic. Known for its exceptional thermal stability and high impact strength, PPE plastic is suitable for components exposed to extreme conditions. Polyphenylene oxide is often used for electrical components in high-heat applications due to its excellent resistance to heat distortion.
This page is for informational purposes only. Fern Plastics provides injection moulding services and does not supply the material.
Polyphenylene Oxide Properties
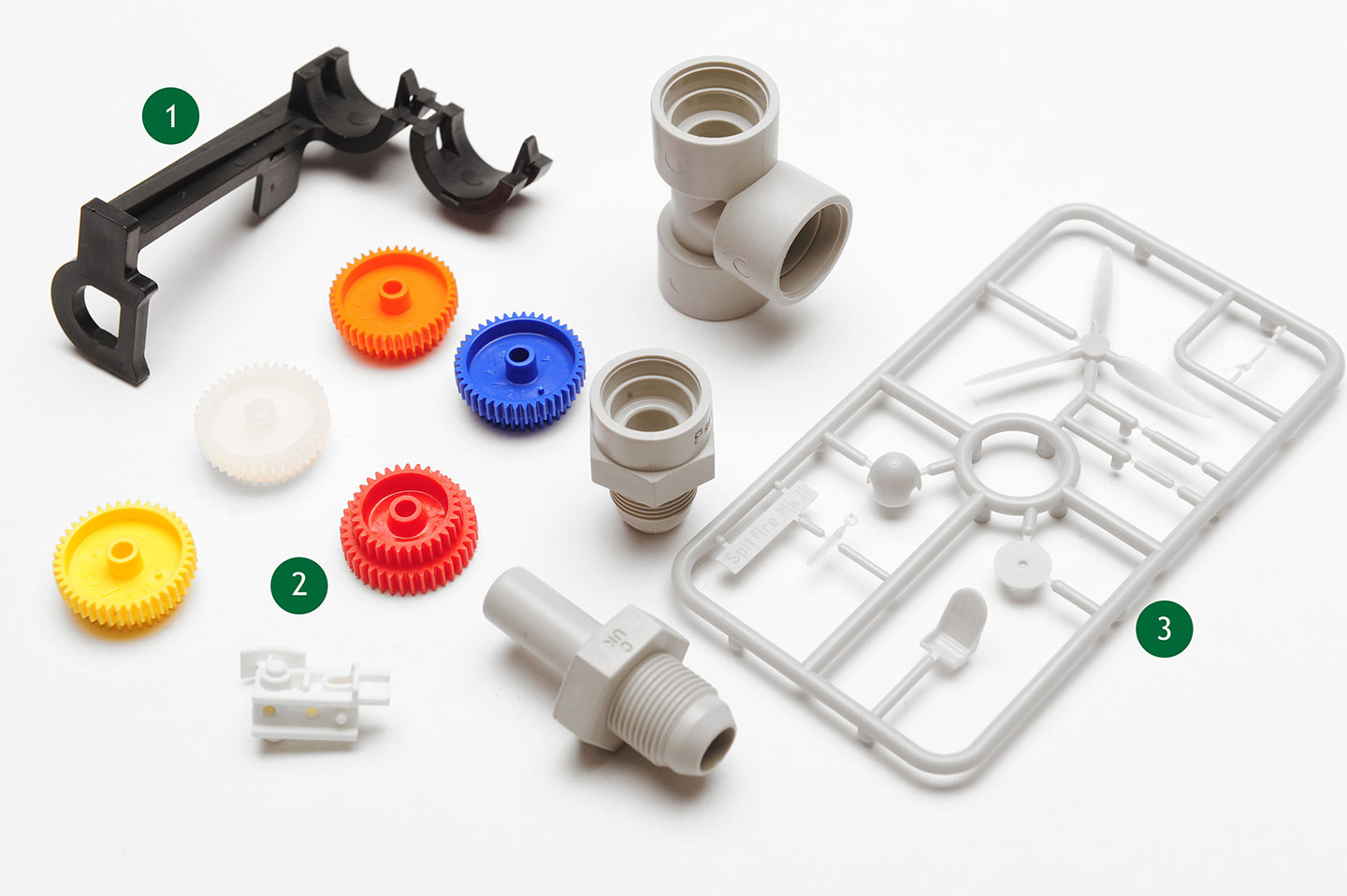
Polyphenylene oxide is a key engineering plastic with a variety of properties that make it a beneficial choice for demanding injection moulding applications. In addition to properties like chemical and flame resistance, PPO material can be blended with other materials to further enhance features like impact resistance while reducing costs.
- Thermal stability
- Dimensional stability
- High impact strength
- Excellent dielectric properties resulting in high insulating resistance
- Heat and flame resistance
- Chemical resistance
- Low relative density
- Low water absorption
Benefits of Using PPO Material in Plastic Injection Moulding
Choosing PPO material for plastic injection moulding can provide manufacturers with a range of advantages from design flexibility to enhanced product performance. Using PPE plastic for injection moulded parts can also enhance product lifespans with impressive chemical and thermal resistance. As an amorphous thermoplastic, polyphenylene oxide is strong with dimensional stability across a varied range of temperatures making it beneficial when heat resistance is essential.
- Non-toxic
- Recyclable
- Transparent
- Low shrinkage
- Good load-bearing qualities at high temperatures
- High heat distortion resistance
- High strength-to-weight ratio
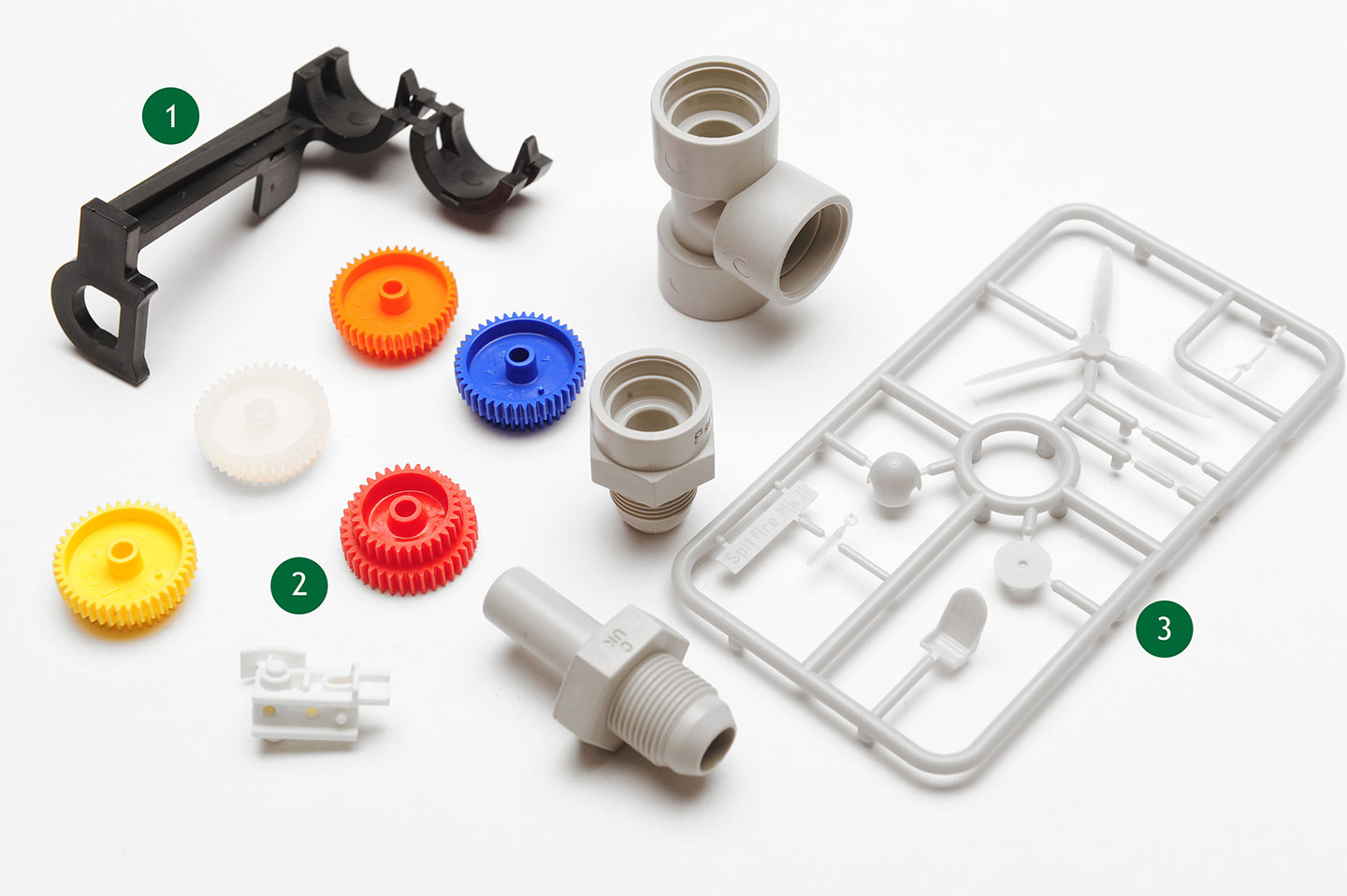
Common PPO Plastic Uses
The versatility of PPO plastic makes it a useful material across a broad spectrum of industries. Its resistance to solvents and acids make it ideal for challenging environments while its stability makes it excellent for structural components.
- Housings and internal components for electrical equipment
- Pump filters
- Shock absorbers
- Computers
- Circuit breakers
- Air conditioning units
- Television components
Disadvantages of Polyphenylene Oxide
Plastic injection moulding with polyphenylene oxide plastic has a few disadvantages that can negatively affect the process. Factors like UV instability and the materials’ tendency to become a thermosetting plastic when stored for long periods are some of the disadvantages manufacturers should be aware of.
- Low fatigue resistance
- Poor fluidity
- It can cost more than other resins
- High melt viscosity
- When exposed to UV light, uncoloured PPO can become yellow
Using PPO Materials for Your Plastic Injection Moulded Project
Known for its exceptional thermal stability, chemical resistance, and lightweight properties PPO or PPE is an excellent choice for plastic injection moulding applications. Whether you’re creating intricate components for the automotive or parts for electronics PPO plastic offers reliability and versatility for high-performance applications.
To learn more about how PPO can enhance your plastic injection moulding project, contact Fern Plastics online or call 01902 758282 to speak with our team of experts. We’ll guide you through the best material choices for your specific needs.