Polyoxymethylene (POM) Injection Moulding
Polyoxymethylene (POM) is a high strength engineering thermoplastic with a semi-crystalline structure. Also known as Acetal and polyacetal, POM is a robust technical plastic with good stability that makes it ideal for making precision components. Acetal plastic also offers low frictional resistance making it suitable for manufacturing products that need to be resistant to wear. Polyoxymethylene is a formaldehyde-based plastic that can be divided into two groups – acetal homopolymer (POM-H) and acetal copolymer (POM-C) each with slightly different properties POM-H (acetal homopolymer) has a lightly higher density and hardness while POM-C offers better chemical resistance.
This page is for informational purposes only. Fern Plastics provides injection moulding services and does not supply the material.
Properties of Polyoxymethylene (POM) / Acetal Plastic
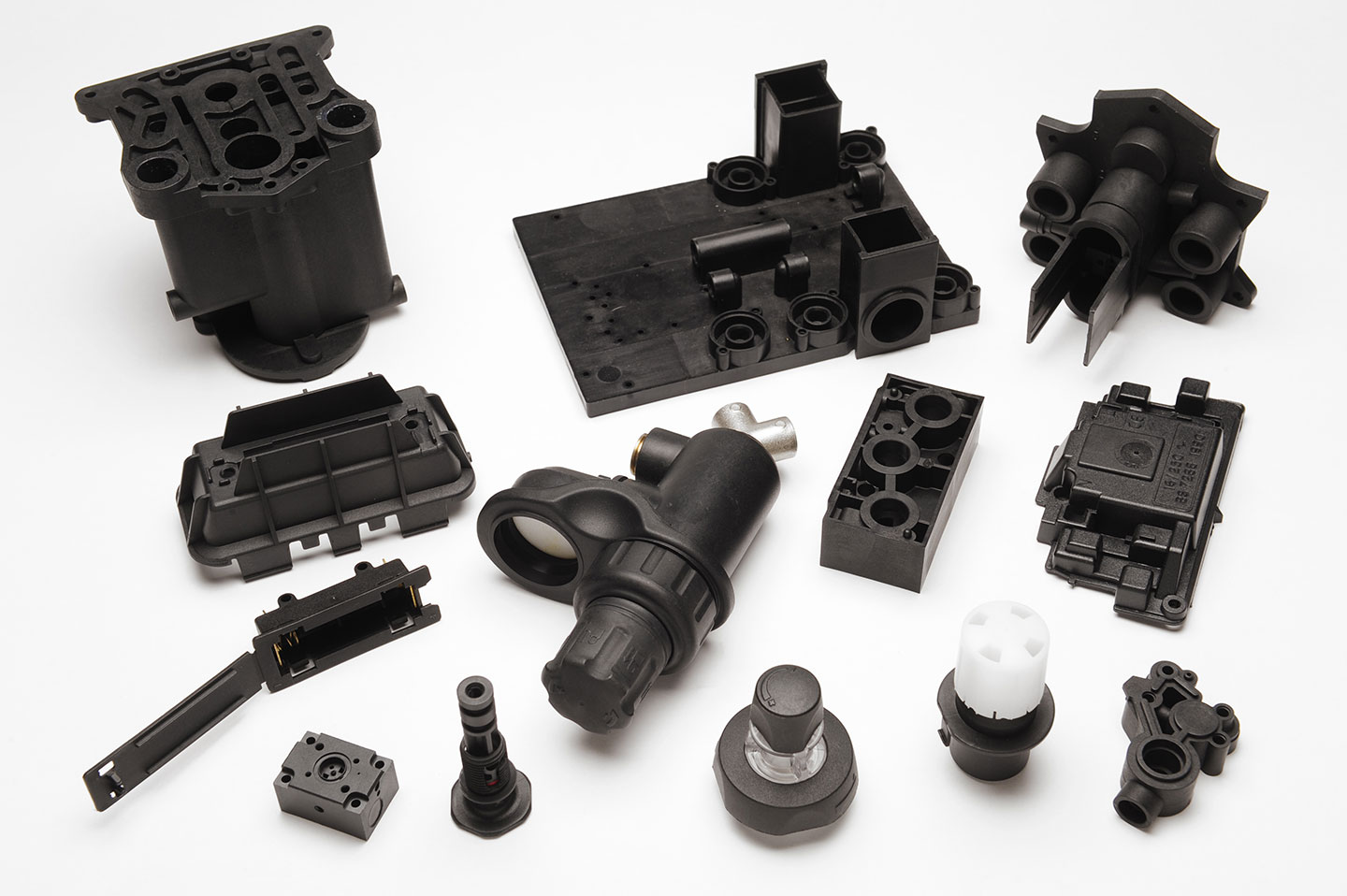
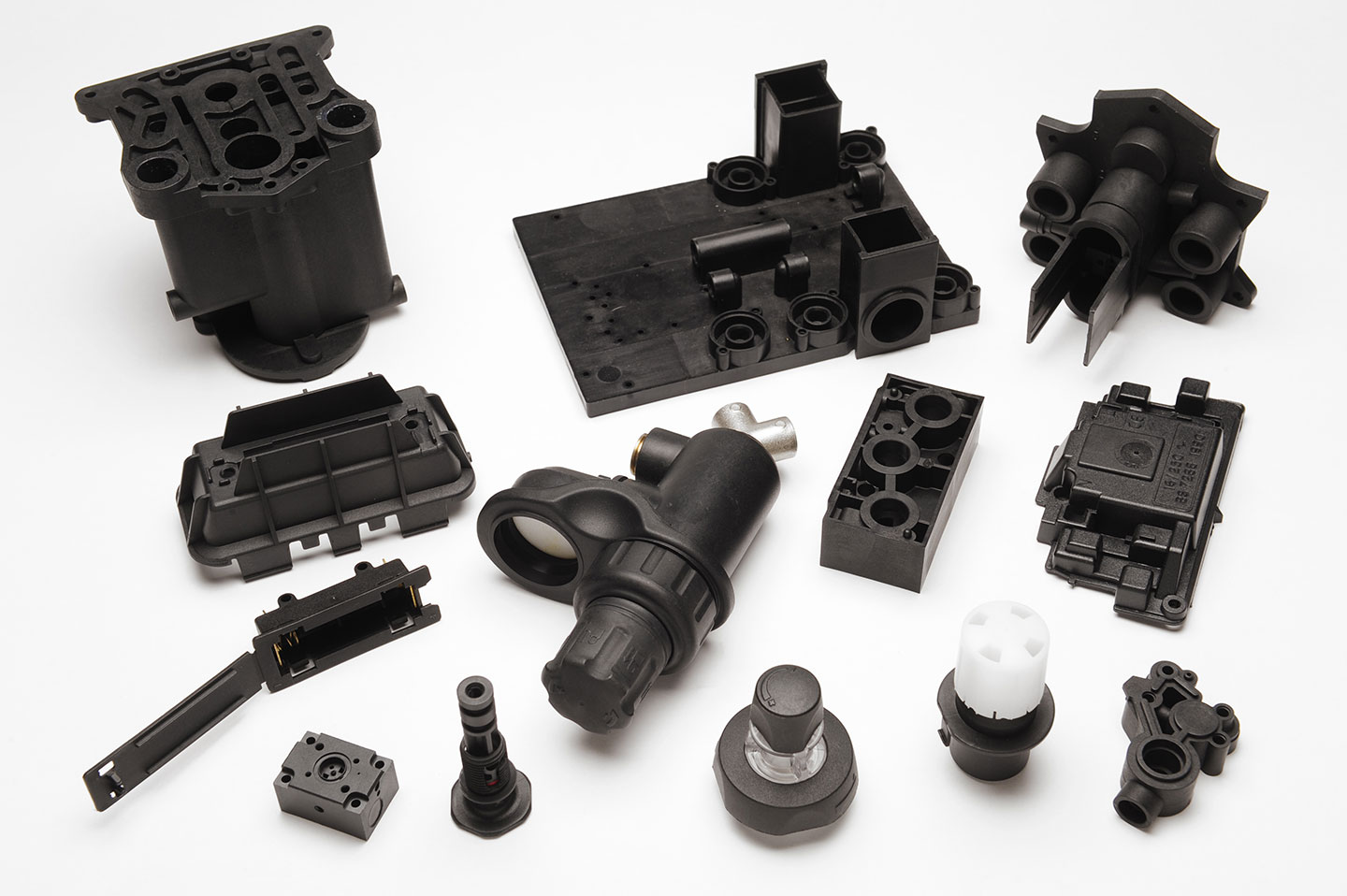
The properties of POM or acetal plastic makes it suitable for manufacturing high quality products with plastic injection moulding. Its excellent elasticity helps it to retain its form while the low coefficient of friction makes it ideal for the smooth operation of moving parts. The mechanical properties and dimensional stability of acetal plastic are maintained by its low moisture absorption and good creep resistance.
- High tensile strength
- Dimensional stability
- High rigidity
- High impact resistance
- Low water absorption
- Good electrical insulating properties
- Thermal stability
Benefits of Using POM Material in Plastic Injection Moulding
There are a range of benefits to ABS injection molding and ABS polymers. Among other useful qualities, acrylonitrile butadiene styrene is a lightweight, inexpensive plastic injection moulding material. When the combination of acrylonitrile, butadiene and styrene are varied, ABS plastics have additional qualities such as flame retardant abs when fire retardant additives are added. Adding other materials to ABS can create grades of ABS with medium to high-impact resistance, high heat resistance and improved ability to be electroplated.
- 100% Recyclable
- Resistant to wear
- Offers good electrical insulation
- Food safe
- Excellent form retaining properties
- Good stability makes it ideal for precision components
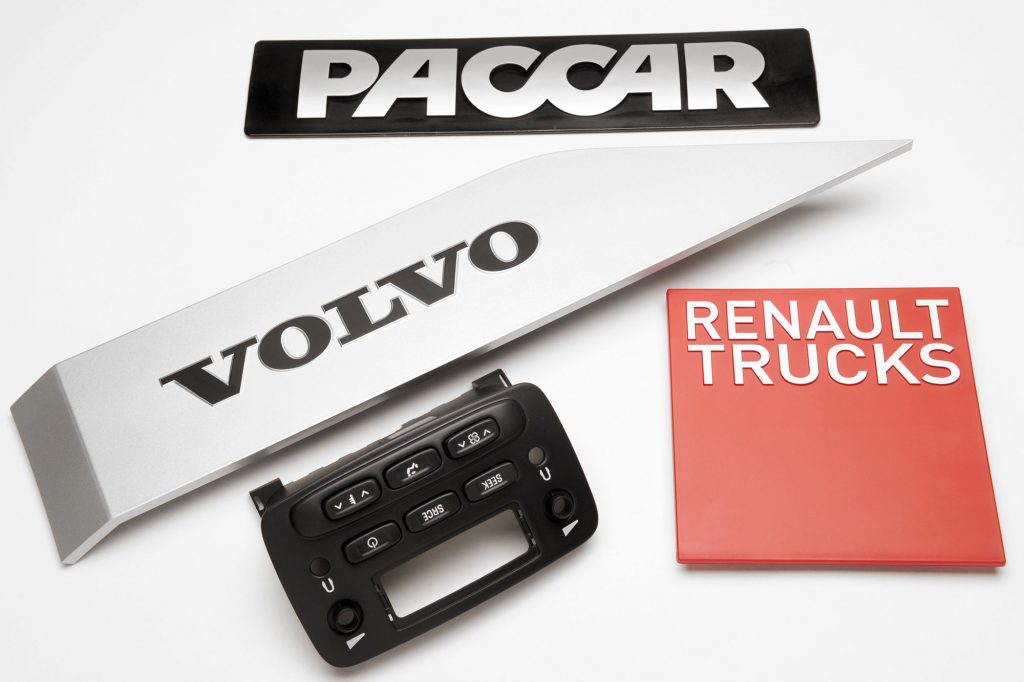
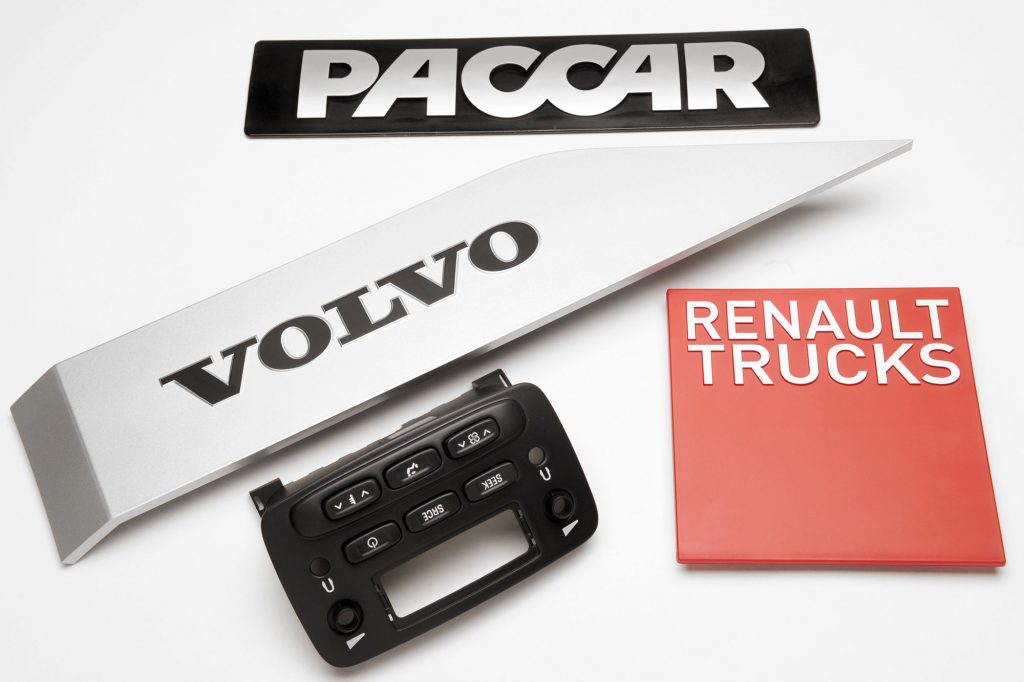
Common Polyacetal Plastic Uses
POM can be used for components requiring long-term reliability and performance when processed using plastic injection moulding. From general consumer products to automotive and high precision parts, the durability and strength of POM plastics makes it a suitable choice across multiple industries.
Gears, valves and other precision parts for the automotive industry
A wide variety of consumer products such as tool handles, toys, sports equipment and clothing zippers
Medical devices like metered-dose inhalers, insulin pens and surgical instruments
Electrical components that require resistance to moisture like insulating components, switches and connectors
Intricate moving parts for watches and clocks
Musical instrument parts such as guitar picks, bagpipes and drumsticks
POM Plastic DisadvantagesÂ
As with all thermosplastics, while there are advantages to using POM, injection moulding polyacetal plastic has some disadvantages that can effect the result and performance of your moulded part.
Can be sensitive to UV exposure
Has a large range of shrinkage
Not suitable for bending or welding due to rigidity
Requires controlled processing conditions as POM degrades at high temperatures and can release formaldehyde gas.
Can become chemically weak when exposed to strong acids
Using POM Materials for Your Plastic Injection Moulded Project
The form retaining properties, high tensile strength and resistance to wear make Polyoxymethylene material a robust and versatile choice for your plastic injection moulding projects. Its ability to produce products that can withstand repeated use and its recyclability make POM injection moulding an option for sustainably minded manufacturers.
For more information about using POM in your injection moulding, contact Fern Plastics now online or by calling 01902 758282.